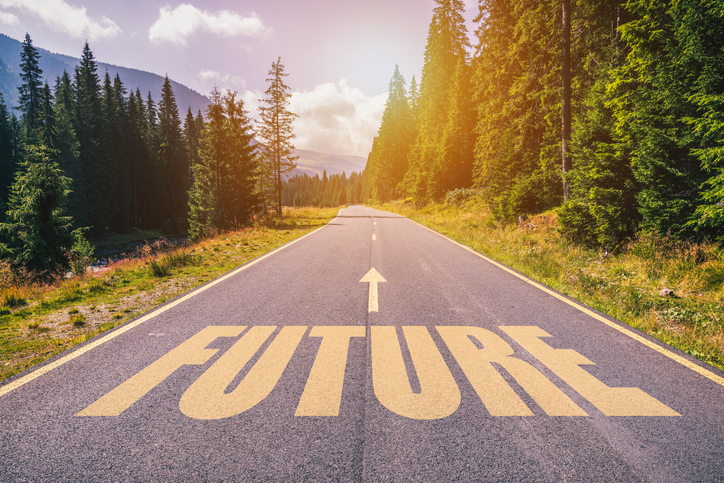
Is it Viable for a Therapist to Start an Industrial Therapy Business? ABSOLUTELY!!! Do it now!!!
February 20, 2019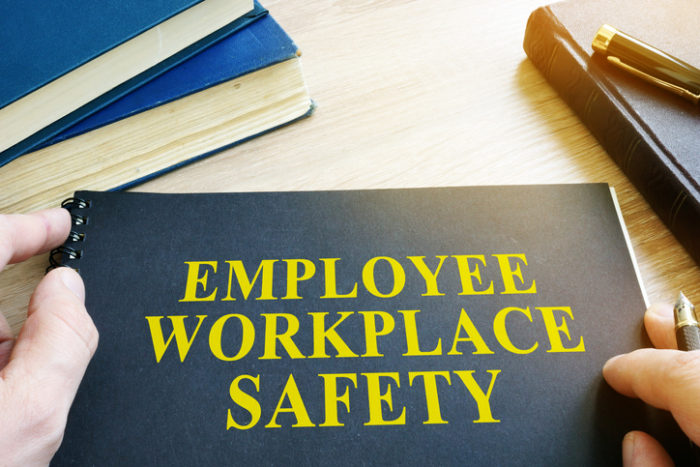
The 8 Occupations with the Highest Incidents of Days Away from Work
May 8, 2019Repetitive motion injuries can result in either temporary or permanent damage to muscles, ligaments, nerves, and tendons. These injuries occur when a person is making the same problematic motion over and over again. One of the most common diagnoses resulting from repetitive motion, is Carpal Tunnel Syndrome (CTS), although other injuries also occur depending on the work that is performed and the characteristics of the individuals that perform it.
Many Employees are at Risk
Even though Carpal Tunnel is often associated with employees who sit at a computer all day, these repetitive motion injuries occur in many other occupations as well. For example: working in a deli using a meat slicing machine, working in food manufacturing including the agricultural beginning to the packaging of products to the preparing and serving in a restaurant, cosmetologists, veterinarians and other workers with animals, physical laborers in construction, light or heavy work in assembly, to name a few. The motions required by the work or vibrations within tools or temperature of the work site in combination with the position forces of the body, can lead to symptoms, diagnosis, and a reportable/recordable injury.
Pay for Prevention or Pay BIG for Treatment
According to the State of California Dept. of Industrial Relations, CAL/OSHA, the average cost per RMI is $40,000. FOR ONE CASE. The cost of an excellent Carpal Tunnel Syndrome prevention program for an entire work force, depending on size of course, can be far less than that and can cut incidence rates by more than half! It also decreases suffering, and results in significant changes within the work site as well as having a positive change domino effect into all the families of those who work there.
If an employee demonstrates or reports ’complications’ related to a repetitive motion they are doing, or is noted to be modifying a tool or rubbing their wrist or neck or other related body part – it is essential to address it right away, for the purpose of avoiding progression any further.
Two primary focus areas to review or have reviewed by qualified individuals:
- Equipment placement: Is the work site equipment set up to best accommodate the workers as it relates to placement of height, distance and Or is its setup based on ‘this is the way it’s always been’.
- Is the worker taught proper techniques for safety and efficiency for their bodies? For example, managers and workers should all be trained in ‘Fight the Five’ for prevention of CTS. There are other primary movements to prevent with other cumulative trauma injuries. These are the 5 positions and movements of the wrist that should be removed from the activity and replaced with other positions when working to prevent CTS:
- No wrist Flexion
- No wrist Ulnar Deviation (bending wrist to little finger)
- No putting hand in Supination (palm up)
- No pressure at the base of the palm
- No physical constriction around the wrist
Employee Assessment Before Returning to Work
When an employee takes medical leave due to these injuries, caution needs to be used as they are returning to work. Employee Return-to-Work physical ability assessments offer an effective way to determine a person’s physical capabilities. This proactive approach reduces the risk of another injury and helps in minimizing costs in the future.
As an employer, it is essential that you assess the workplace and have your employees trained not only in what we commonly think of as ‘safety practices’ but also the efficient and safe use of their body during these work activities. Between the two of these, you bring about significant reduction of all types of injuries. Prevent the injuries – save the $40,000 PER INJURY (direct and indirect costs).
At KEY Functional Assessments Network, we understand the impact that injuries can have in a workplace. Our team has developed proven systems for employers to implement employee screenings and education – improving safety and productivity. Contact us to learn about the available solutions.